Producing fiber-reinforced concrete
What makes Tecwill shotcrete technology different?
Mixing high-quality fiber reinforced concrete or shotcrete requires precise control over material dosing and weighing, concrete mix temperature and slump.
For each concrete batch Tecwill's equipment ensures:
- High-accuracy weighing with Tecwill's “flying” weighing system
- Better aggregate moisture control with the Tecwill's OptiMoist system
- Optimized control over concrete mix slump and temperature
We deliver comprehensive, proven fiber dosing equipment for modern shotcrete production.
- Lower operational costs
- Reduce cement usage
- Decrease CO2 emissions
Tecwill’s innovative on-conveyor fiber feed system reduces mixing time and eliminates fiber clumps.
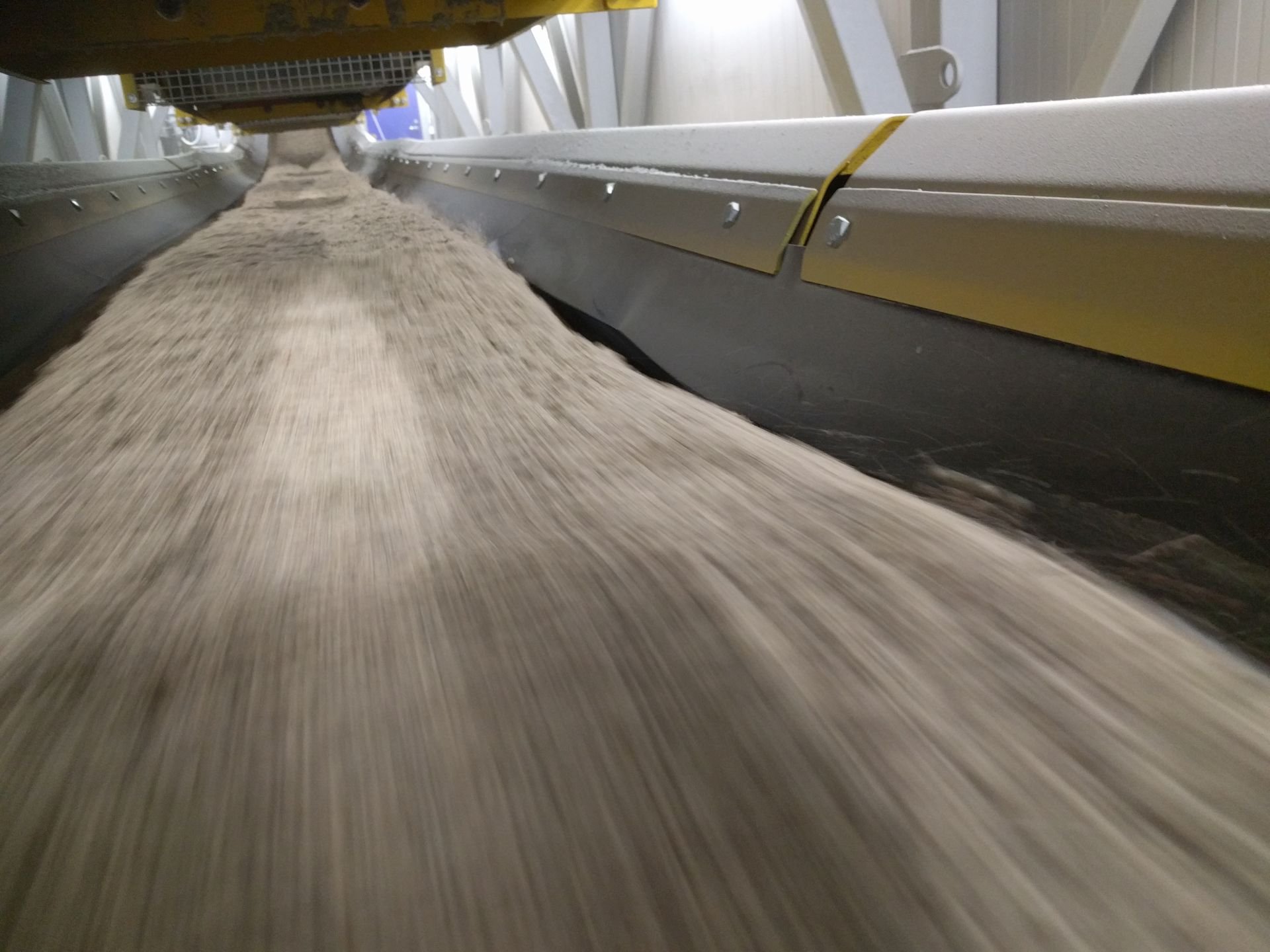
- Shorter mixing time for increased plant capacity
- Reduced fiber clumping
- Minimized problems with spraying machines
Fiber equipment
The fully automated "flying" weighing system doses steel and/or plastic fibers directly on top of the flowing aggregates, ensuring proper spreading and efficient premixing .
Watch the videoWhen different types of fibers are used, the fiber unit can be delivered with several separate dosers.
Fibers can be fed into the plant mixer or directly to truck mixer drum.
Automatic fiber dispensing system
Any concrete batch plant can be equipped with an automatic fiber dosing system to precisely measure and dose the required amount of fiber into the concrete batch.
Typically, fibers are added to the ready-mixed concrete in a concrete mixer. Alternatively, a mixer bypass method dispenses the fibers directly into a truck mixer.
Our automatic fiber dispensing system includes:
- A fiber dispenser with all needed accessories
- A batch control system that accurately dispenses fibers according to mix design
- Optional enclosure for winter operations
The Tecwill “flying” aggregate weighing and dosing system allows fibers to be dosed at the same time as aggregates. Fibers are added to the moving aggregate flow, where they are pre-mixed with the aggregates. This approach provides many advantages over other systems, including:
- Shorter mixing time because fibers have been pre-mixed with the aggregates
- Reduced mixer wear due to shorter mixing times
- Better concrete quality because of the homogenous distribution of fibers
- No fiber clumps in the concrete
- Fewer problems with shotcrete spraying machines
- Improved tunnel lining quality
Polypropylene (PP) fibers are widely used in shotcrete and concrete floors. Because they are very light, they require a special dosing system. Our solutions for PP fibers include:
- Manual dosing system for 1, 2 or 5 kg fiber bags
- Fully automatic bag dispenser system for bagged fibers
- Fully automatic dispenser system for loose fibers
Color pigments in either liquid or powder form can be added to concrete. Each for requires a specialized dosing system.
Our liquid dosing system consists of storage tanks, pumps, scales and pipelines. We can deliver 1 to 6 color tanks for each plant, depending on customer requirements.
Powder pigments are dosed either as powder or granules, depending on the application. Both forms are dosed using a screw conveyor (auger) from the super bag storage bin to the scale.
The measured batch is then transferred from the scale to the mixer by a pneumatic conveying system. The dosing process is integrated with the control system for automatic operation.
READ MORE ABOUT SHOTCRETE AND FIBER DISPENSING
The mixing of fiber concrete or shotcrete causes anxiety for many concrete plant operators. Since fiber concrete is usually only produced for special projects, the concrete plant and equipment should be designed to work in the best possible way.
This Tecwill blog provides deeper insights and answers to common questions about shotcrete and fiber dispensing.
Testimonials, case studies and blogs
Testimonials and blogs about our deliveries of shotcrete batching plants to various tunneling and mining projects.
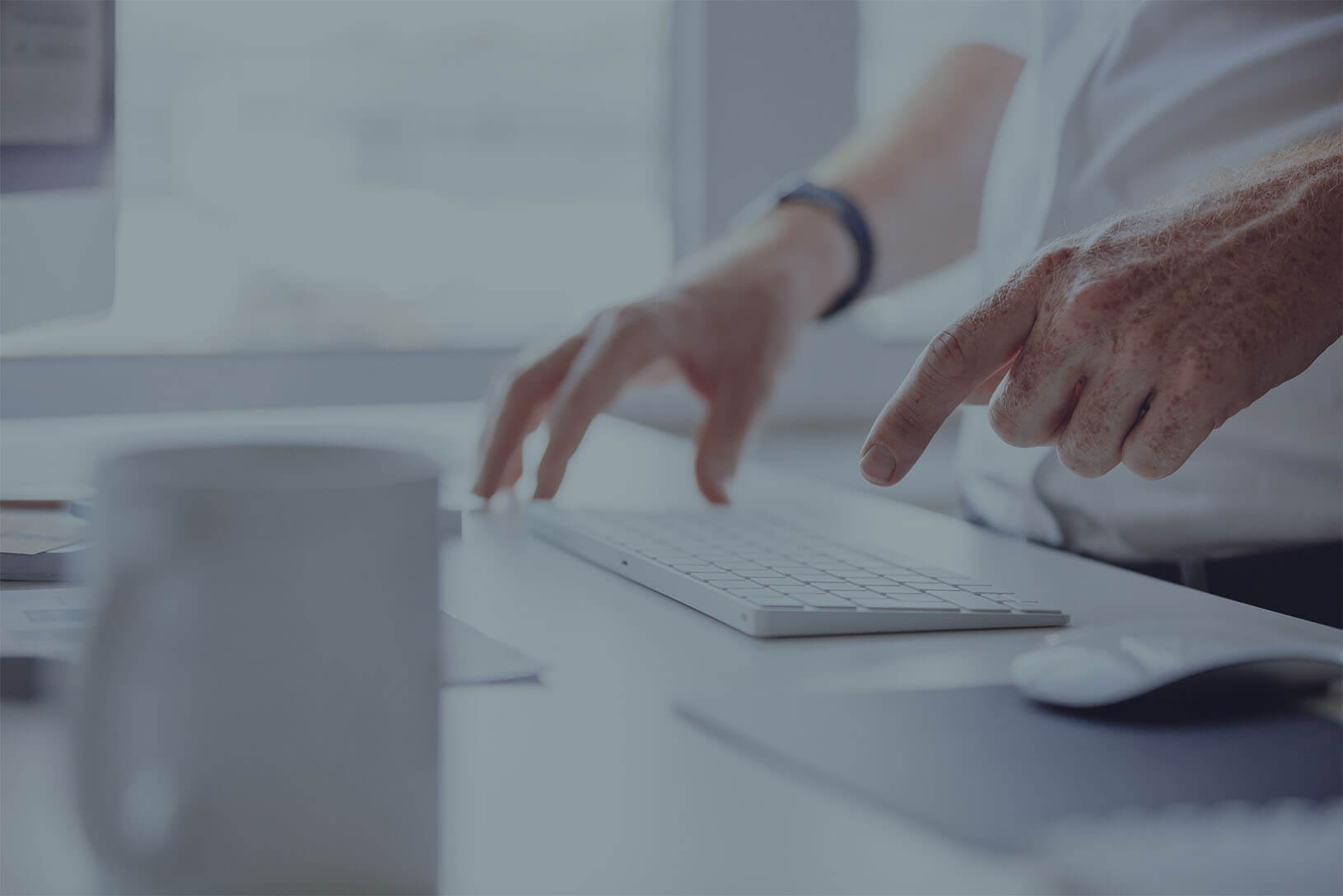