TABLE OF CONTENTS
Revolutionary batch plant solutions for 3D concrete printing
3D concrete printing companies often struggle with concrete quality issues. The batch slump varies, and printers are prone to breaks. Instead of concrete, printing companies are forced to use mortar, which is more expensive and has a very high cement content. Ultimately, this results in higher carbon emissions.
With our 3D-Mix concrete batch plant, you can effortlessly print houses with concrete.
By incorporating a bigger aggregate size of up to 1/2” (12 mm), you achieve enhanced volumetric stability of the concrete. This, in turn, enables increased printhead speed and makes it possible to construct multi-floor houses.
Our 3D-Mix concrete batch plant:
- Can mix concrete instead of mortar
- Reduces out-of-spec concrete
- Ensures fewer printer breaks
- Saves cement and reduces carbon emissions
Tecwill 3D-Mix plant set-up
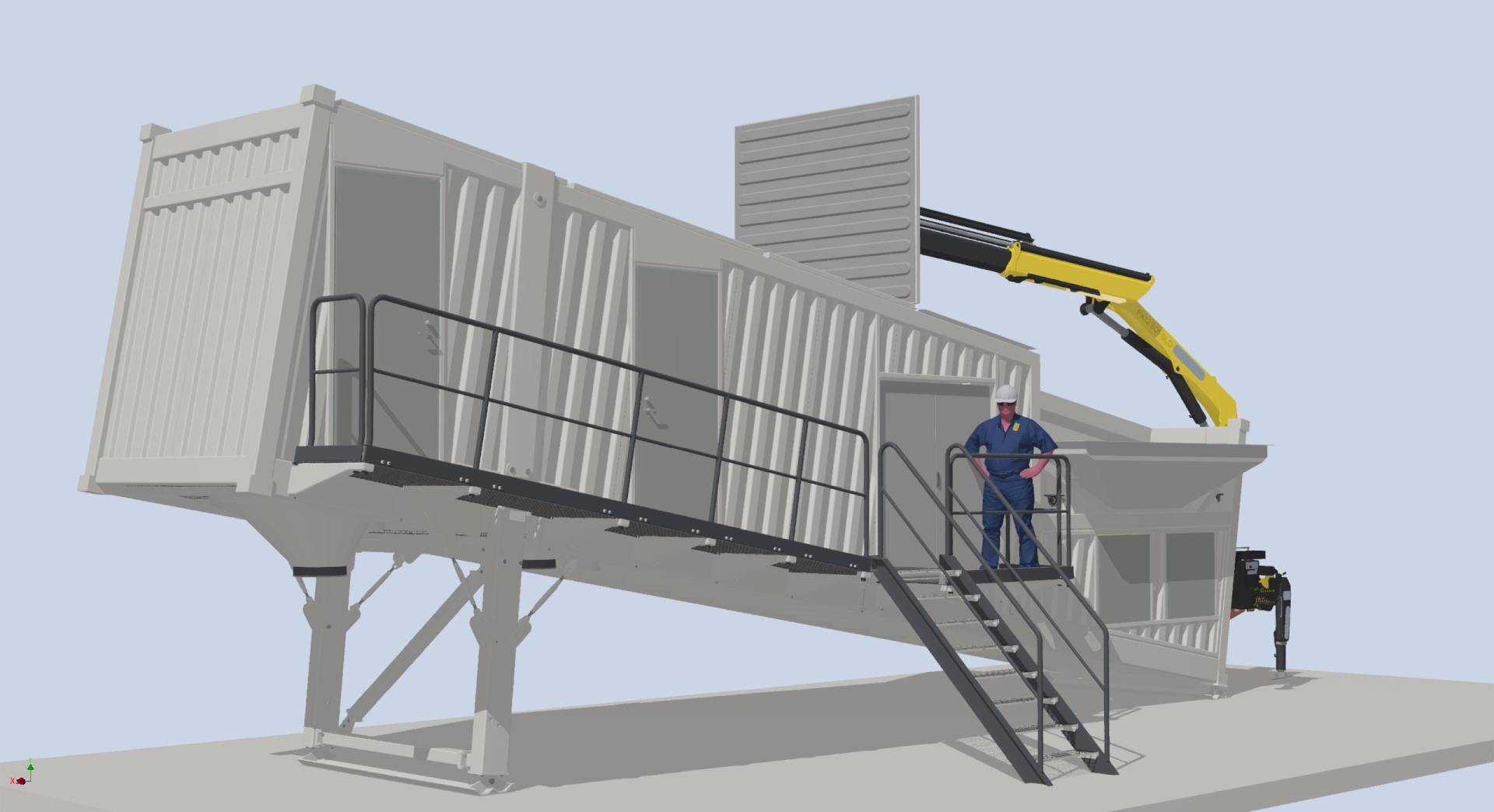
3D-Mix plant for both ready-mix and 3D printer concrete
- Concrete for 3D printing
- Ready-mix concrete from the foundation, walls and other structures to the floors
- Paving concrete for sidewalks and roads
- Self-consolidating concrete
- Precast concrete
- Zero-slump concrete
- Colored 3D concrete using powder, C pigment or granule pigments
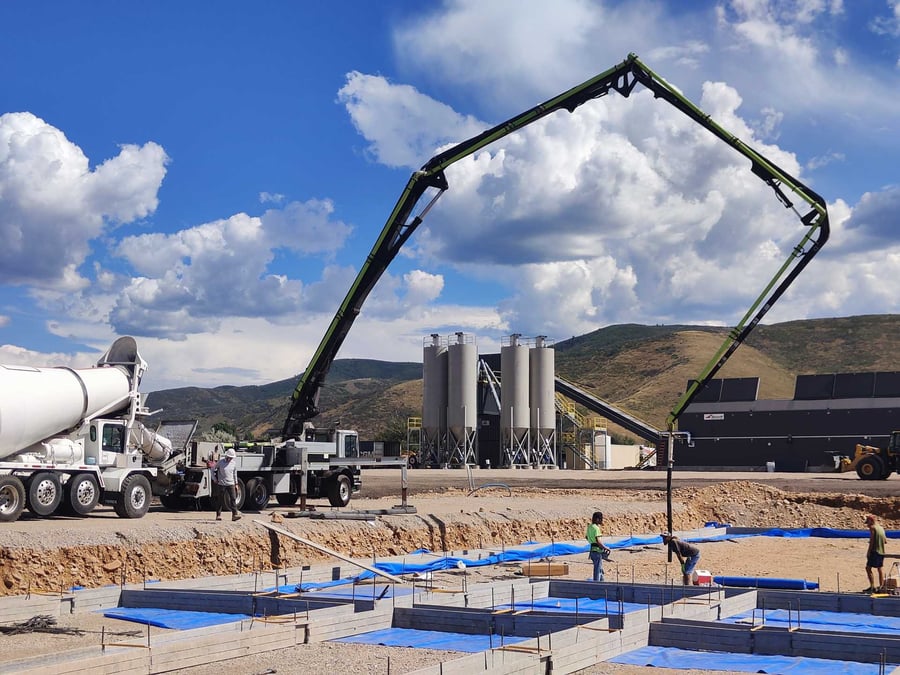
Why choose Tecwill – how are we different?
Instead of using cement-heavy mortar, the 3D-Mix plant allows for the use of concrete.
Tecwill’s high-precision AI-controlled “flying” weighing system with OptiMoist moisture control.
- Bigger aggregate size of up to 1/2” (12 mm)
- Better strength of the printed structure
- Less cement and admixtures
- Correct slump
- Possibility of building multi-floor printed houses
Unique Tecwill 3D-Mix plant superiorities reduce CO2 emissions.
Unlike conventional technology, a Tecwill 3D-Mix plant can reduce carbon emissions.
- Mixes concrete instead of cement-heavy mortar
- Improves aggregate moisture control
- More accurate weighing
- Better temperature control
Pre-wired and tested self-erecting super-mobile 3D-Mix plant in a single unit.
Tecwill preassembles the 3D-Mix plant at its own factory. This includes pre-wiring, piping, enclosure and plant testing. As a result, you get:
- Fast set-up time
- On-board admixture and water tanks
- Automatic delivery of multiple liquid admixture scales
- Pre-wired for US 480 V, Canada 575 V UL/CSA approved and Europe 400 V
FAQs
These are questions we’re often asked. We hope you find these helpful. If you still have a question we haven’t addressed, please contact us directly.
When producing 3D-printed concrete – not mortar – it is necessary to achieve sufficient pumpability and buildability characteristics. In 3D printing, these go far beyond the usual standards for conventional concrete.
The plants must work with high cement content and aggregates of up to 1/2” (12 mm). They also must use multiple admixtures with automatic dosing and accurate (not volumetric) scales. Plus, integration of the accelerator at the nozzle head enables rapid setting of the mix.
The process of producing 3D-printed concrete mandates an exceptional level of precision in the dosing and weighing of all materials. Simultaneously, it involves accurate moisture management and temperature control. A small mistake in slump quality can ruin the batch, block the printer or compromise the structural integrity.
A common mistake occurs when concrete producers attempt to use a standard batch plant for 3D-printed concrete production. Such plants are unable to meet the required tolerances, leading to operational challenges.
We have developed a completely new “flying” aggregate weighing system equipped with improved OptiMoist aggregate moisture measuring technology that ensures accurate dosing of raw materials.
Normally, mortar is used to print houses. It is a very expensive cement-sand mix. At the same time, it is brittle and lacks sufficient tensile capacity. Because of the high cement content, the price of such a house is unnecessarily expensive.
With our technology, you can use concrete for 3D-printed houses. Concrete has higher aggregate content and less cement. The price of such a house is lower, and less carbon is emitted during production.
With Tecwill’s 3D-Mix plant, you can produce all types of concrete mix designs needed for the project, including:
- Concrete for 3D printing
- Ready-mix concrete
- Roller-compacted concrete
- Precast concrete
- Bigger aggregate size of up to 1/2” (12 mm) can be used
- Lower cement content and smaller carbon footprint
- Improved volumetric stability of concrete due to coarse aggregate
- Decreased hydration heat and shrinkage due to coarse aggregate
- Greater stability and strength of the printed structures
- Stronger multi-floor printed houses
Concrete batch plant models
The 3D-Mix concrete mixing plant is a cutting-edge production unit designed specifically for 3D printing applications. This compact, enclosed plant offers maximum flexibility and prints stronger, lower-cost structures – a game-changer for 3D concrete printing.
See productThe Arcamix versatile hybrid concrete plant is well suited to urban environments and can be used to produce various types of concrete. It fits on a small footprint, is enclosed and low profile. Thanks to its modular construction, the plant is easy to set up and relocate.
This multipurpose concrete production plant offers a capacity of up to 150 m3/h (200 yd3/h).
See productThe Cobra concept represents the latest approach to concrete production. The same solution can be used as a mobile on-site or a central-mix plant. The plant is quick to install and easy to move to a new location.
The Cobra plant is suitable for the production of various types of concrete and has a capacity of up to 120 m3/h (160 yd3/h).
See productTecwill in brief
- 30 years of experience designing and manufacturing concrete plants
- Our technology significantly reduces CO2 emissions from concrete production
- Global operations
- Head office, assembly factory and testing facility in Joensuu, Finland
Want more information?
The 3D-Mix batch plant is a game-changer in the 3D concrete printing industry.
Read the blogWatch the Arcamix concrete plant delivery video.
Watch the videoThe Arcamix concrete batch plant mixes concrete in downtown Gothenburg, Sweden.
Read more