Local supplier with a long history
For over 70 years, Hellestad Sandtak of Telemark County in southern Norway has been in business, focusing primarily on delivering natural gravel, crushed aggregate and ready-mixed aggregate-based concrete for the county. When they realized their existing plant was coming to the end of its operating life, they decided to invest in a new concrete mixing plant to be located at the same site. Risks of longer production interruptions had been increasing.
They knew from extensive experience in the field that modern, up-to-date production methods would enable them to achieve higher efficiency and better use of manpower.
Photo: Hellestad Sandtak AS
Choosing a concrete batch plant with a good reputation
Hellestad Sandtak reached out to Tecwill at the end of December 2021 to begin discussions about a new concrete mixing plant. Negotiations progressed quickly. By the start of February 2022, the company had placed an order for a new Cobra C80 concrete mixing plant.
Hellestad Sandtak knew that Tecwill’s Cobra C80 concrete mixing plant has a good reputation in the European market. It is considered to be versatile, easily portable and well equipped for winter operations. Therefore, they decided the Cobra C80 plant best suited their needs.
Although Hellestad Sandtak had not purchased any Tecwill equipment previously, our comprehensive offer, efficient production capacity, compact layout and reliable technical solutions influenced their final choice.
We visited their site at the beginning of the project to be sure we fully understood their needs. Thereafter, we agreed it was more reasonable to continue all negotiations remotely. All plant delivery details were discussed by phone, over Teams and through emails, which is very untypical for projects of this scope and size.
Aggregate bin storage capacity increased by 60%
Hellestad Sandtak’s site is an almost completely flat sand field with plenty of options for positioning the concrete batch plant. Still, they wanted to utilize a slight slope as part of the ramp structure to increase the capacity of the aggregate bins.
We recommended building a two-meter-high natural ramp. This increased aggregate storage capacity by 60% and allowed storing approximately 300 tons of aggregate in the Cobra C80 plant’s silos. Although the silos are larger than usual, a large amount of aggregate from the customer’s own gravel pit can be stored there for heating and weather protection during the winter.
Additionally, Hellestad Sandtak specified a mixer with a minimum batch size of 1.85 m3 (2,4 yards) which Cobra C80 could easily provide.
Project management of steel
Commissioning of the Cobra C80 took only 6 days including plant enclosure and aggregate and water heating system. Then testing of the batch control system started. Technically, the Cobra C80 plant filled all the requirements Hellestad Sandtak had specified at the start.
“The pocket conveyor, which lifts aggregate into the immediate container, operates well,” says Olav Hellekås, CEO of Hellestad Sandtak AS.
“Both Mikko and Arttu, along with other installation supervisors from Tecwill, did a great job. They know how to install and commission a concrete plant with professional expertise and steely project management skills. The plant looks really good!” he sums up.
Batch plant delivery scope
The delivery scope for the project included the Cobra C80 plant itself, Tecwill planetary mixer, hydraulic discharge hatch, cement scale with a separate filter, Walter high-pressure mixer washer, "flying" aggregate weighing and dosing system, a separate recycling water scale, 4 x 50 m3 (65 yards) elevated aggregate bins, separate dust-free electrical central room, aggregate moisture measurement system and a camera system.
Want more information?
Download the Cobra concrete plant brochure
Watch the installation of the Cobra concrete mixing plant.
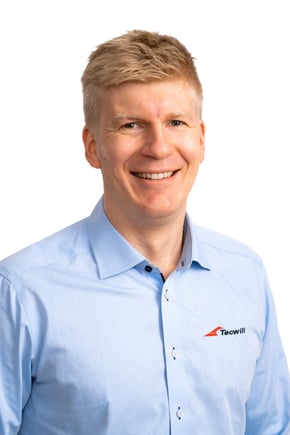