SUSTAINABILITY AND CARBON REDUCTION
TABLE OF CONTENTS
How does Tecwill help reduce the carbon dioxide emissions of the concrete industry and help it reach net zero?
The concrete industry is undergoing unprecedented change to achieve decarbonization. There is no shortcut. We must take responsibility for all our activities.
Even though Tecwill is among the top in the industry when it comes to carbon reduction and sustainability, we constantly work to improve our products and operations. Decarbonization is an important priority in our product development. That’s why we continue to innovate new technologies and solutions to support our customers in their decarbonization transition.
Our technologies are tested and used around the world. Here are some examples of how we improve carbon neutrality and get closer to net zero.
Examples of Tecwill’s carbon-reducing technologies
The more accurate “flying” aggregate weighing and dosing system improves weighing deviation and requires very limited space. This allows more accurate dosing and lower aggregate bin construction than in a conventional solution.
- Possibility to save cement by up to 30 kg/m3 (50 lb/yd3)
- Less steel and space needed for structures
- Significant savings in fuel and wheel loader operating costs
The AI-based dosing and weighing algorithm enables faster throughput with more repeatable batch quality. Improved material weighing provides the correct slump and a better dosing deviation.
- Lowers production costs
- Saves cement
- Reduces CO2 emissions in concrete production
Improved aggregate moisture measuring with more accurate material dosing and weighing leads to significant savings in concrete production. The right amount of aggregates and water in each concrete batch shortens the mixing time and allows the cement content to be reduced in the mix design.
- Less energy
- Correct slump
- Less cement
Frequently asked questions
These are questions we’re often asked. We hope you find these helpful.
If you still have a question we haven’t addressed, please contact us directly.
Low-carbon concrete has a lower global warming potential (GWP)3 compared to standard concrete.
Low-carbon concrete is produced by reducing the cement content of concrete and using supplementary cementitious materials like:
- Fly ash
- Blast furnace slag
- Calcined clay
- Silica fume
- Natural pozzolans
- Metakaolin
- Geopolymers
Depending on the dosage of these additions, the carbon footprint of concrete can be reduced by up to nearly 70%.
Recycled aggregate and sand, crushed concrete and reclaimed water are also common alternative materials used in low-carbon concrete production.
The production of cement as a raw material for concrete is a major source of carbon dioxide emissions. Tecwill’s technologies have been specifically developed to reduce the amount of cement used in concrete, thereby reducing CO2 emissions:
- Our “flying” aggregate weighing system ensures accurate dosing of raw materials
- OptiMoist improves aggregate moisture measuring to ensure the correct use of slump and cement
- AI-based dosing and weighing
Our solutions improve the energy efficiency of concrete plants and increase water recycling to cut back on CO2 emissions.
When manufacturing our products, we reduce our own environmental impact by using recycled steel and developing new ways to minimize our material consumption.
- Using less steel
- Carrying out pre-wiring and full testing at our factory before delivery
- Providing factory-assembled enclosures
Our concrete plants are hybrid plants. The same solution is suitable for all types of concrete mix designs, including:
- Ready-mix concrete
- Shotcrete
- Roller-compacted concrete
- Zero-slump concrete
- Self-consolidating concrete
- Precast concrete
The main challenges and barriers to implementing better carbon dioxide reduction strategies in the concrete industry include:
- Old-fashioned production plants
- “Open-concept” dry batch plants prone to dust emissions and high cement content
- Fear of implementing new technologies
- Limited availability and high price of new cementitious materials
- Lack of standardized regulations and incentives
- Adoption of sustainable practices
Concrete batch plants typically have environmental impacts related to:
- Carbon emissions
- Air emissions – dust
- Noise pollution
- Water usage and recycling
- Admixture leakage
- Generation of waste materials
- Handling of waste concrete
- Oil leakage
Concrete producers can contribute to carbon reduction and environmental sustainability by implementing measures such as:
- Using better concrete production technology
- Selecting alternative fuels or energy sources
- Optimizing energy efficiency
- Reducing water consumption
- Improving dust and noise control
- Adopting recycling or waste management practices
Carbon reduction at a concrete batch plant
Concrete production is a major contributor to carbon emissions with significant environmental implications. The process of manufacturing cement, a key component of concrete, involves the release of carbon dioxide (CO2), accounting for approximately 8% of global CO2 emissions.
Improved technology, low-carbon concrete and sustainable production practices, including recycling and reducing emissions and material waste, are crucial to minimizing the carbon emissions associated with concrete production.
How can low-carbon technologies be used at a concrete plant?
There are many ways to reduce the carbon impact of the batch plant, vehicles, components and processes. Most of the carbon reduction and carbon removal innovations are focused on three key areas: more efficient batch plants, selecting low-carbon fuels and using low-carbon materials.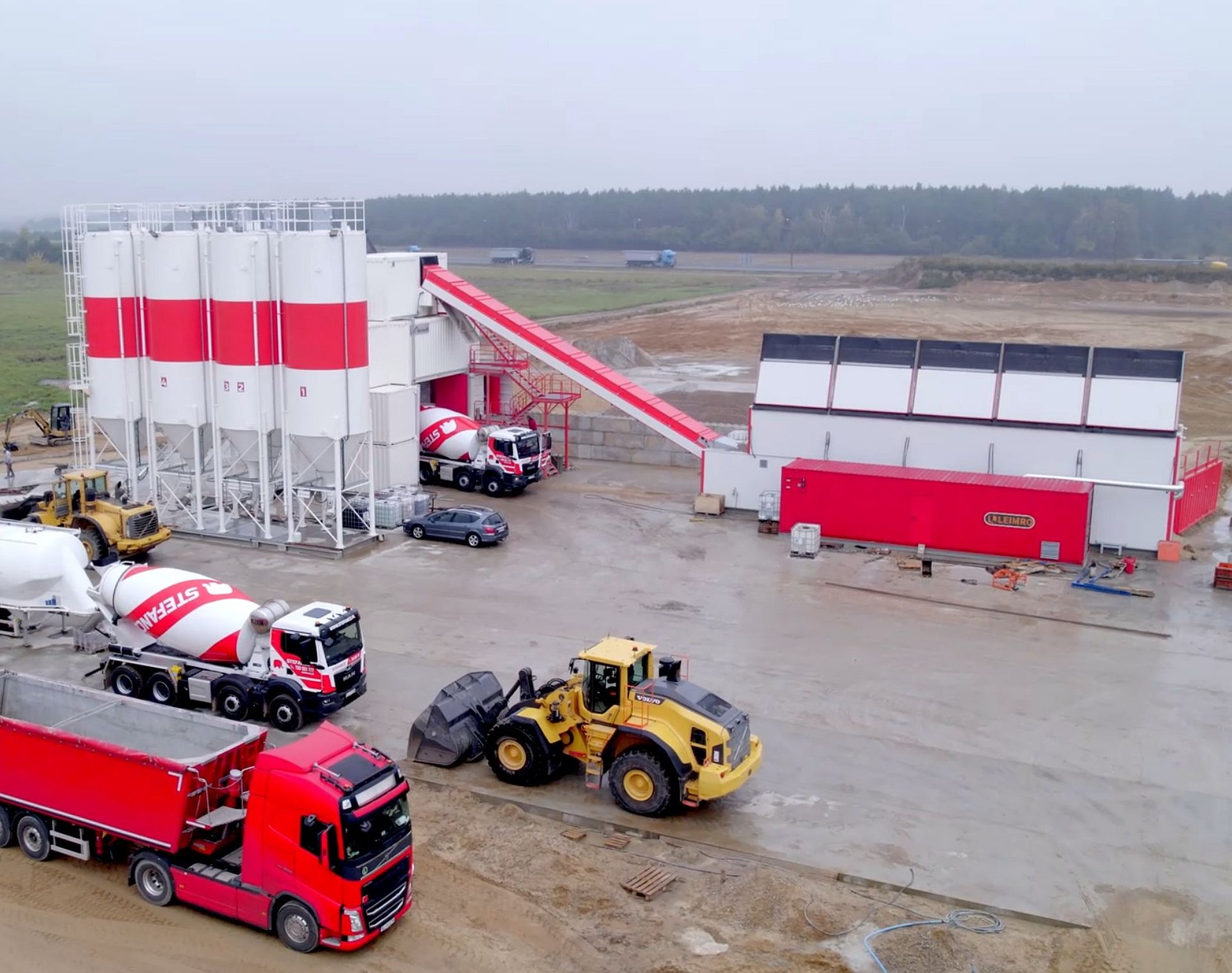
New innovations to reduce carbon emissions at a concrete plant
Low-carbon concrete
Supplementary cementitious materials
- Low-carbon cement
- Slag
- Fly ash
- Low-carbon blended cements
- Geopolymer cement
- Activators
Better plant operation
Equipment and production methods
- More accurate weighing
- Better moisture management
- Effective heating/cooling
- Wet mix instead of dry batch
- Better enclosure
- New operating practices
More efficient logistics
Plant location and trucks
- On-site batch plant instead of permanent plant
- Enclosed concrete plant
- New low-carbon fuels
- Optimized transport and deliveries
Want more information?
Read the blog on how better technology helps to reduce carbon footprint.
Read the blogAn on-site concrete plant and a short transport distance reduce the carbon footprint of a downtown project in Gothenburg, Sweden.
Read moreThe Cobra plant mixes concrete for the largest wind turbine park in the world.
Read more